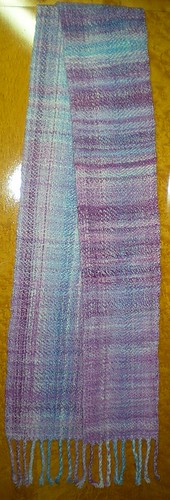
I gave an overview of reading weaving drafts in my last rigid heddle post, to help you identify 2-harness (or if you prefer, 2-shaft) table/floor loom drafts and figure out how to thread them on your rigid heddle loom with just one heddle.
When you add a second heddle, the possibilities multiply.
For starters, you can use a yarn that is twice as fine -- warping both heddles as described by Ashford here and by Schacht here lets you use both together. So, if you have 8, 10, and 12-dent reeds, besides being able to use yarns that are 16, 20, and 24 wraps per inch (plain weave sett/ends per inch is typically 1/2 the wraps per inch of the yarn; thicker will be more tough, in both senses of the word, and thinner will be more gauzey -- the technical term is sleazy, as the threads on too loose a sett will slide over one another), you can now use yarns that are 32, 40, and 48 wraps per inch -- that would make a wonderfully thin, drapey stole or fine silk scarf. Aaahh.
But it turns out, there are a whole host of interesting 3-harness (3-shaft) patterns out there, with names and everything. I was flipping through the May/June 1989 Handwoven (thanks to blogless Kathy, a local weaver extraordinaire), and lo-and-behold, an article about 3-harness weaving!
My first foray into 2-heddle weaving on my Glimakra Emilia rigid heddle loom was a basic 2/1 twill, though I turned it into a point and reversed treadling order half way through, so it looks like the wave-echo of a center diamond, a bit like this: <<<<>>>>
Of course, given it was woven at a very loose sett and fulled, and I used a multi-color handspun 2-ply, that diamond design is a bit lost. But, it's there, and if I looked closely I could see it.
Now, the draft of a 2/1 twill looks like this:

You can see that it uses just three harnesses, and has a straight tie-up.
So, when I threaded the heddles, I threaded the front slot (to match harness 1), the front hole(to match harness 2), and the back hole (to match harness 3). Anything threaded in the front heddle goes through slots in the back heddle, so they are only raised and lowered by the front heddle. Also, anything threaded in the back heddle's holes must go through a slot in the front heddle. See the Ashford and Schacht writeups mentioned above for good pictures of threading the front heddle's threads through the back heddle's slots.
For the treadling, first I had to lift harness 1; since it was the slot thread, I "lifted" it by lowering both heddles to the down position. Second, lift harness 2, which is the front heddle. And third, lift harness 3, the back heddle. So, it was both down; front heddle up/back heddle neutral; front heddle neutral/back heddle up; repeat until woven.
Other interesting patterns you can do in a 3-harness weave include:
- point twill: turn the twill around, so you go 1-2-3-2-1-2-3-2-... repeating across, and treadle the same way (1-2-3-2-1-2-3-2-...). Leigh has a nice post on 4-harness twills showing how they turn into point, rosepath, and broken (herringbone) patterns.
- rosepath, which is an extended point twill that looks like a path of roses; this is pretty as a stripe in an otherwise plain-weave tea towel.
- herringbone twill, another extended point twill
- a basic waffle weave -- this is interesting because it does not have a simple straight tie-up, so you would need to work out the lifting/lowering pattern to ensure the right warp threads were up. But you can do that -- read on for advice :)
- summer & winter -- Ashford's 2-heddle writeup shows how to do this, along with its cousin, Taquete.
- Bronson lace -- this lace is interesting because it uses the first harness on a multi-harness loom at the "tie-down"; so you can have lace with just 3 harnesses. Other related laces (huck and Swedish lace) move the tie-down around with the lace pattern. Here's a Margaret Atwater article, The Bronson Weave Four Ways, talking about having 3 spot positions with 4 harnesses -- with our two heddles, we have "3 harnesses" so can have 2 spot positions.
- Spot Bronson, cousin of Bronson lace -- this has a nice texture, I've made some washcloths with it.
- Krokbragd -- a weft-faced weave from Norway, traditionally woven with three colors.
- warp floats and their cousins, deflected warp -- if you put your warp floats on the back heddle's holes, then you can control when they float and when they don't. By weighting them separately from the rest of the warp, you can also deflect them for even more visual interest in your weaving.

- Front heddle slot is harness 1
- Front heddle hole is harness 2
- Back heddle hole is harness 3
- both up: harnesses 2 & 3 up
- both down: harness 1 up
- front up/back neutral: harness 2 up
- front down/back neutral: harnesses 1 & 3 up
- front neutral/back up: harness 3 up
- front neutral/back down: harnesses 1 & 2 up
In the picture above, you can see I have the front heddle up and the back heddle in neutral; so I have harness 2 up, and harnesses 1 (the slot-only warp threads) and 3 (the back heddle holes' threads) down.
So, have at it -- look through Margaret Davison's tome A Handweaver's Pattern Book, Anne Dixon's colorful The Handweaver's Pattern Directory
, and pick out the simple 3-harness twills, rosepaths, and more from Margaret Windeknecht's Color-and-Weave
and Color-and-weave II -- or whatever weaving books are on your bookshelf or at your local library.
There are 760 3 harness drafts on Handweaving.net -- page down to "Keyword search", leave the keyword box empty, and enter "3" in the minimum shafts and maximum shafts boxes, then click "search". That should be plenty to keep you busy for a while (grin).
A topic to mention when you map a 3 harness pattern to the rigid heddle loom is, what to do about the rigidity of your heddles. On a harness loom, the heddles move, so you can thread 3 in a row on harness 3 without leaving a big gap; but on your rigid heddle loom, you'd be skipping a lot of slots and holes if you spaced them out. So consider grouping two warp threads in the same slot or hole to keep your ends per inch where they need to be if the pattern you are mapping repeats the same harness next to itself.
Pay attention to the ends per inch, rather than blindly grouping all repeats in the same path -- some spreading may be called for. Consider this draft, for example. With its 1-1-1-1-2-3-2-repeat threading, I'd be likely to start by grouping the 1's in pairs, skipping the intermediate rigid heddle slots/holes for 2 and 3, then do 2, 3, skip the open 1, 2 again, and repeat. If it gave me the ends per inch I wanted, I'd keep going that way. A sample would definitely be called for, to see if it would turn out the way I wanted it to look.
If spacing of the warp is a concern in the final weaving, sample first, and remember to wet finish your sample -- the yarns may move into the position you want, or they may track badly -- it's better to learn from a small skein of sample yarn than to have to throw the completed project in the Goodwill box because it didn't turn out like you had hoped.
~~
If you'd like a very mathematical look at 3 harness weaves, I came across this Mathematical Research Paper on the topic: On 3-Harness Weaving: Cataloging Designs Generated by Fundamental Blocks Having Distinct Rows and Columns, by Shelley L. Rasmussen, in the electronic journal of combinatorics 15 (2008), #R1
~~
posted 18 February 2009 at http://askthebellwether.blogspot.com/